Memtech S.A. proponuje kompleksową budowę instalacji termicznego przekształcania odpadów komunalnych oraz osadów ściekowych w oparciu o sprawdzoną technologię.
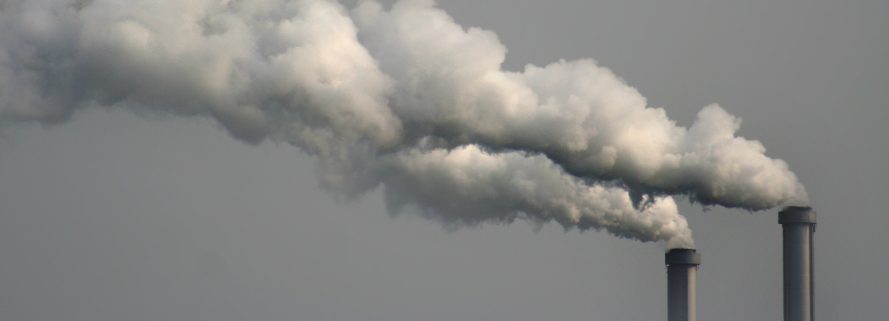
Instalacja będzie wyposażona w:
- układ kotłowy,
- układ podawania odpadów,
- układ zasilania paliwem wspomagającym,
- układ powietrza zasilającego, chłodzącego, recyrkulacji spalin oraz AKPiA,
- układ oczyszczania i odprowadzenia spalin,
- układ odprowadzenia popiołu,
- układy pomocnicze kamienia wapiennego i materiału inertnego,
- układ sterowania i AKPiA,
- układ monitoringu spalin,
- turbozespół parowy,
- chłodnie wentylatorowe,
- stację uzdatniania wody,
- układ rurociągów i pomp,
- podłączenie bloku do systemu energetycznego,
- system rozliczania energii.
W ramach przedsięwzięcia konieczne będzie wybudowanie takich obiektów budowlanych, jak:
- kotłownia,
- maszynownia,
- komin stalowy,
- silos odpadów, zapewniający ciągłość pracy instalacji.
Opis układów technologicznych oraz podstawowych urządzeń
a
Układ kotłowy
Zasadniczym elementem proponowanej instalacji do termicznego przekształcania odpadów biodegradowalnych jest układ kotłowy, w którym następują w sposób ciągły, proces suszenia i odgazowywania odpadów, a następnie proces spalania powstałego gazu pirolitycznego oraz karbonizatu, zapewniając tym samym maksymalne wykorzystanie energii chemicznej zawartej w dostarczanym paliwie. W skład układu kotłowego wchodzą:
- zespół obrotowej komory suszenia i odgazowywania,
- zespół kotła fluidalnego,
- konstrukcje wsporcze komory obrotowej i kotła fluidalnego.
W obrotowej komorze suszenia i zgazowania realizowany jest proces suszenia, gazyfikacji oraz częściowej neutralizacji siarki i chloru przy pomocy rozdrobnionego węglanu wapnia. Proces w zależności od stopnia zawilgocenia i zawartości popiołu w przekształcanych odpadach po termicznym zainicjowaniu przebiega autotermicznie w atmosferze redukcyjnej, podtrzymywany przez wysokoenergetyczne źródło energii cieplnej. Produkty gazyfikacji z komory obrotowej przepływają do komory fluidalnej, gdzie mieszają się z powietrzem „pierwotnym”. Komora obrotowa jest wykonana w postaci rury stalowej, wyłożonej warstwą materiału termoizolacyjnego i termoodpornego, z osadzonymi pierścieniami tocznymi i napędowymi, osadzonej na rolkach nośnych i oporowych ramy nośnej, posadowionej na dodatkowej stalowej konstrukcji nośnej. Napęd komory obrotowej zapewnia układ motoreduktorów oraz przekładnia łańcuchowa. Paliwo zasadnicze w postaci odpadów podawane jest podajnikiem płyty czołowej. W płycie czołowej znajduje się również palnik olejowy lub gazowy inicjujący i podtrzymujący proces suszenia i odgazowania. Zespół kotła fluidalnego jest konstrukcją złożoną, składającą się z:
- komory fluidalnej,
- komory separacji,
- komory dopalania, oraz ciągu konwekcyjnego.
Dno komory fluidalnej zamknięte jest od dołu rusztem fluidalnym z dyszami oraz układem komór zasilania gazem fluidyzacyjnym.
Gaz pirolityczny powstający w komorze obrotowej przepływa do komory fluidalnej Proces spalania gazów pirolitycznych w komorze spalania jest rozciągnięty na całą wysokość komory fluidalnej poprzez rozdzielenie powietrza niezbędnego do spalania na powietrze „wtórne” i powietrze „trzecie”. Dzięki temu rozdziałowi powietrza, możliwe stało się ograniczenie temperatury w jądrze płomienia spalających się gazów pirolitycznych do poziomu 1200°C ÷ 1300ºC.Ograniczenie temperaturowe i ograniczenie koncentracji powietrza (cząstek N2, O2) w strefie spalania, pozwala utrzymać proces tworzenia się termicznych NOx na możliwie niskim poziomie. Do spalania gazów pirolitycznych wykorzystywane jest zanieczyszczone powietrze, pobierane z odciągów wentylacyjnych układu rozładunku, przygotowania i podawania wsadu do komory obrotowej, dzięki czemu następuje likwidacja wszelkiego rodzaju przykrych zapachów.
Powstały w komorze obrotowej karbonizat i popiół zsypują się do dolnej części komory fluidalnej, gdzie łącznie z doprowadzonym z zewnątrz materiałem inertnym (np. piasek kwarcowy), tworzą złoże fluidalne, którego fluidyzacja następuje w wyniku przepływu gazu fluidyzacyjnego, składającego się ze spalin z recyrkulacji oraz powietrza. Dla uzyskania prawidłowych parametrów pracy złoża fluidalnego w fazie rozruchu kotła uruchamiane są dodatkowo rozruchowe palniki olejowe lub gazowe. W złożu fluidalnym proces spalania karbonizatu przebiega w temperaturach niższych od temperatury mięknienia popiołu, tj. 750°C÷900°C. W procesie spalania karbonizatu następuje prawie całkowita neutralizacja siarki, chloru oraz niektórych metali ciężkich do związków obojętnych chemicznie, usuwanych z popiołem. Zawartość części palnych w usuwanym popiele dennym jest mniejsza od 1%. Popiół stanowi pełnowartościowy surowiec budowlany, a w szczególnych przypadkach może stanowić doskonały surowiec do produkcji nawozów sztucznych.
Spaliny na wyjściu z komory fluidalnej są „pierwotnie” oczyszczone z par metali ciężkich i alkalicznych oraz z lotnego popiołu i koksiku, poprzez zastosowanie festonu górnego. Następne oczyszczanie spalin z zanieczyszczeń stałych następuje w komorze separacji oraz na wejściu do komory dopalania, gdzie zastosowano feston dolny. W komorze dopalania, w obecności płomienia paliwa wysokokalorycznego następuje całkowite, katalityczne dopalenie śladowych ilości pirolitycznych gazów palnych oraz lotnego koksiku, dzięki czemu spaliny opuszczające komorę dopalania pozbawione są jakichkolwiek gazów palnych oraz palnych części stałych. Spaliny nie zawierają dioksyn, furanów, wielopierścieniowych węglowodorów aromatycznych (WWA), cząstek sadzy (Corg) oraz par metali ciężkich i alkalicznych. Spaliny na wejściu do powierzchni ogrzewalnych kotła mogą zawierać śladowe ilości chlorowodoru, chlorków, tlenków fosforu, potasu itp. Ograniczenie zawartości substancji szkodliwych dla otoczenia następuje w trakcie procesu spalania poprzez dawkowanie substancji neutralizujących zanieczyszczenia siarkowe chlorowe oraz poprzez stworzenie wielostopniowego procesu spalania gazów pirolitycznych w takim reżimie temperaturowym oraz przy takiej ilości powietrza, przy których powstawanie NOx jest optymalnie minimalne (poniżej 150mg/nm3).
Spalanie karbonizatu w złożu fluidalnym i wiązanie siarki przez związki wapniowe odbywa się w określonych przedziałach temperaturowych, przy określonej koncentracji tlenu w gazie fluidyzacyjnym, w taki sposób, że zawartość części palnych w usuwanym popiele jest poniżej 1%, a zawartość tlenków siarki na wylocie z czopucha kotła jest mniejsza od 100mg/m3.
Odbiór ciepła następuje poprzez ściany szczelne, stanowiące parownik kotła. W ciągu konwekcyjnym kotła montowany jest dwustopniowy przegrzewacz pary, podgrzewacz wody oraz podgrzewacz powietrza. W przypadku zastosowania dodatkowo turbozespołu ORC, w ciągu konwekcyjnym kotła możliwe jest usytuowanie podgrzewacza oleju termalnego.
Kocioł fluidalny podwieszony jest do konstrukcji nośnej kotła za pomocą regulowanych zawieszeń, pozwalających na swobodne wydłużanie się kotła do dołu, a jednocześnie umożliwiających wyregulowanie położenia wlotu komory fluidalnej w stosunku do komory obrotowej.
b
Układ przyjęcia, magazynowania i podawania odpadów
Nie istnieje konieczność budowy dużego magazynu odpadów przeznaczonych do termicznego przekształcania. Należy natomiast określić minimalny zapas tych odpadów, który będzie gromadzony w silosie, w bezpośrednim sąsiedztwie instalacji, zabezpieczającym ciągłość pracy instalacji.
Podstawowa oferta zawiera układ monitoringu i ważenia dostarczanych do zakładu odpadów i biomasy oraz badania ich właściwości w celu określenia udziału frakcji biodegradowalnej, mającej bezpośredni związek z systemem rozliczania świadectw pochodzenia energii.
Powietrze z układu przyjęcia i magazynowania (z hali przyjęć, znad silosu magazynowego), obarczone wszelkiego rodzaju przykrymi zapachami będzie zasysane przez wentylatory i wykorzystywane jako powietrze niezbędne do procesu spalania w kotle fluidalnym, dzięki czemu merkaptany będące źródłem dokuczliwych zapachów będą likwidowane w procesie spalania, jako palne węglowodory.
Transport odpadów z silosu magazynowego do układu kotłowego zapewni układ zgarniaczy i podajników transportowych. Podajniki transportowe zastosowane w układzie będą w wykonaniu szczelnym, co wyeliminuje przykre zapachy w budynku kotłowni. Wsad podawany do układu kotłowego będzie podlegał ważeniu w trakcie podawania.
c
Układ zasilania paliwem wspomagającym
Proces termicznego przekształcania odpadów biodegradowalnych wymaga, w zależności od stopnia zawilgocenia, zastosowania dodatkowego paliwa wspomagającego w postaci oleju opałowego lub gazu ziemnego. Paliwo dodatkowe jest niezbędne w procesach:
- zainicjowania procesu suszenia i pirolizy w komorze obrotowej oraz utrzymanie stałej temperatury tego procesu, co jest szczególnie istotne dla odpadów o dużej wilgotności,
- zainicjowania i podtrzymania płomienia spalania gazów pirolitycznych w komorze fluidalnej,
- zainicjowania i podtrzymania płomienia w komorze dopalania,
- podtrzymania temperatury układu kotłowego w przypadku awarii układu podawania odpadów.
- rozgrzania złoża fluidalnego przy rozruchu instalacji w celu uzyskania optymalnych warunków jego pracy oraz zainicjowania spalania karbonizatu,
W instalacji istnieje również możliwość zastosowania zastępczego paliwa wspomagającego w postaci ciekłych biopaliw z zastosowaniem specjalistycznych instalacji palnikowych, powstałych na podstawie własnych, opatentowanych rozwiązań.
d
Układ powietrza zasilającego, recyrkulacji spalin oraz AKPiA
Układ powietrza zasilającego palniki wspomagające Proces suszenia i pirolizy zachodzi w komorze obrotowej przy ograniczonej ilości tlenu, w celu powstrzymania nadmiernego wzrostu temperatury. Powietrze dostarczane jest jedynie do palnika płyty czołowej w celu zainicjowania i utrzymania procesu suszenia i pirolizy. Powietrze układu zasilającego palniki wspomagające zasila ponadto palniki grzania złoża fluidalnego oraz palniki podtrzymujące w komorze fluidalnej oraz komorze dopalania. Układ powietrza spalania Powietrze niezbędne do procesu spalania karbonizatu oraz gazu pirolitycznego, prowadzonego w kotle fluidalnym podlega rozdziałowi i ścisłemu dawkowaniu. Pozwala to na ograniczenie temperatury w jądrze płomienia spalających sie gazów pirolitycznych poniżej 1300°C. Ograniczenie temperaturowe i ograniczenie koncentracji powietrza ( cząstek N2 i O2) w strefie spalania, pozwala utrzymać proces tworzenia się termicznych NOx na niskim poziomie. Powietrze używane do spalania gazu pirolitycznego oraz karbonizatu pobierane jest z znad układu przyjęcia i magazynowania odpadów, co w zdecydowany sposób ogranicza uciążliwość przykrych zapachów. Układ recyrkulacji spalin W celu zapewnienia właściwej pracy złoża fluidalnego i utrzymania jego właściwej temperatury, przy ściśle określonej ilości powietrza podawanego do spalania karbonizatu, do komór zasilających złoże fluidalne podawany jest gaz fluidyzacyjny, tj. mieszanka powietrza oraz spalin pochodzących z recyrkulacji. Strumień i skład gazu fluidyzacyjnego podlega monitorowaniu i regulacji. Spaliny z recyrkulacji wykorzystywane są również do doszczelnienia płyty czołowej komory obrotowej. Układ powietrza sterowania i AKPiA Układ zapewnia powietrze do układów sterowania oraz AKPiA, jak również do zdmuchiwaczy sadzy oraz zdmuchiwaczy popiołu.
e
Układ oczyszczania i odprowadzenia spalin
Spaliny z kanału wylotowego kotła trafiają do urządzeń odpylających. W instalacji przewidziano odpylanie dwustopniowe. Wstępne oczyszczanie następuje w cyklonie, wyposażonym w dozownik celkowy do odbioru popiołu. Oczyszczanie zasadnicze następuje w filtrze workowym typu FLAT BAG. Wysyp pyłu z filtra następuje poprzez dozownik celkowy. Odbiór zanieczyszczonego popiołu następuje poprzez przenośnik ślimakowy do hermetycznych pojemników. Dzięki procesowi „pierwotnego” oczyszczania spalin w układzie kotłowym, ilość zanieczyszczonego popiołu odbieranego z filtrów „wtórnego” oczyszczania spalin jest zminimalizowana. Zastosowanie powyższych urządzeń gwarantuje osiągniecie poziomu emisji pyłu poniżej 8mg/nm3 przy 11% O2.
W szczególnych przypadkach, np. spalania odpadów poszpitalnych, materiałów niebezpiecznych, możliwe jest zastosowanie dodatkowych urządzeń oczyszczania spalin, zapewniających spełnienie wymagań emisyjnych w zakresie zawartości metali ciężkich oraz dioksyn i furanów. Jako opcja dodatkowa może znaleźć tutaj zastosowanie skruber i płuczka z zastosowaniem mleczka wapiennego.
W przypadku przekroczenia wartości granicznych zawartości metali ciężkich lub innych zanieczyszczeń, popiół lotny pochodzący z układu oczyszczania spalin podlega zestaleniu w betonowe bloczki i przekazaniu na składowisko odpadów.
Instalacja wyposażona jest we własny wentylator wyciągowy oraz kanał odprowadzający spaliny do komina elektrociepłowni.
f
Układ odprowadzenia popiołu
Instalacja wyposażona jest w układ odbioru popiołu dennego. Popiół denny powstający w złożu fluidalnym komory fluidalnej oraz w komorze separacji, odbierany jest poprzez lej przesypowy złoża fluidalnego układem przenośników do kontenera popiołu dennego, skąd trafia na składowisko leżakowania przed wysłaniem do odbiorcy (np. producenci przemysłowych materiałów budowlanych). Układy pomocnicze W instalacji zastosowano układy pomocnicze:
- Układ podawania materiału inertnego do złoża fluidalnego (np. piasku kwarcowego), zapewniający możliwość stworzenia złoża oraz utrzymywania jego struktury w trakcie eksploatacji.
- Układ podawania węglanu wapnia do komory obrotowej, w strefę procesu suszenia i zgazowania oraz do procesu spalania karbonizatu. Układy wyposażone są we własne zasobniki i układy podawania.
g
Układ sterowania i AKPiA
Instalacja posiada komputerowy system sterowania pracą wg ustalonego algorytmu technologicznego, obejmujący wszystkie urządzenia. Stacja operatorska umieszczona jest w nastawni centralnej.System sterowania i wizualizacji zapewnia automatyczną pracę urządzeń oraz pełny nadzór nad ich pracą, diagnozowanie usterek i awarii oraz raportowanie dla dokumentowania pracy urządzeń i przebiegów zdarzeń. System sterowania posiada zdolność archiwizacji i analizy parametrów pracy z możliwością bezpośredniej ingerencji w przypadku awarii lub odstępstw od założonego algorytmu.
h
Układ monitoringu spalin
Instalacja wyposażona jest we własny układ monitoringu spalin. Pomiary dokonywane są w kanale doprowadzającym spaliny do komina EC. Układ monitoringu spalin podlega ścisłemu nadzorowi i archiwizacji i podłączony jest do układu sterowania. Zgodnie z Rozporządzeniem Ministra Środowiska z dnia 4 listopada 2008 r. (Dz. U nr 206, poz. 1291) w sprawie wymagań w zakresie prowadzenia pomiarów wielkości emisji oraz ilości pobieranej wody, instalacja zostanie wyposażona w ciągły monitoring gazów odlotowych obejmujący:
- prędkość przepływu spalin,
- pomiar temperatury
- pomiar ciśnienia,
- pomiar zawartości wilgoci,
- pomiar zawartości tlenu,
- pomiar zawartości pyłu,
- pomiar zawartości SO2,
- pomiar zawartości HCl,
- pomiar zawartości Corg,
- pomiar zawartości NOx,
- pomiar CO,
- pomiar HF,
- ciągłą rejestrację oraz wyliczanie emisji rocznej
Emisje substancji szkodliwych
Instalacja do termicznego przekształcania odpadów biodegradowalnych w kogeneracji spełnia standardy zawarte w rozporządzeniu Ministra Środowiska z dnia 22 kwietnia 2011r. w sprawie standardów emisyjnych z instalacji (Dz. U. Nr 95, poz. 558), wg którego wielkości dopuszczalnych stężeń zanieczyszczeń w gazach odlotowych z nowych instalacji termicznego unieszkodliwiania odpadów przedstawia tabela 1 (zgodnie z załącznikiem nr 5 rozporządzenia). W/w standardy odnoszą się do warunków umownych (temperatura 273 K, ciśnienie 101,3 kPa i gazu suchego, tj. o zawartości pary wodnej nie większej niż 5g/kg gazów odlotowych, przeliczonych na 11% tlenu w spalinach). Wytwarzany popiół, jako odpad wtórny zgodnie z & 5 pkt 1 Rozporządzenia Ministra Gospodarki z dnia 21.03.2002 r., (Dz.U. nr 37 poz. 339 z późniejszymi zmianami) w sprawie wymagań dotyczących prowadzenia procesu termicznego przekształcania odpadów będzie zawierać poniżej 3% węgla organicznego i może być wykorzystany do wytwarzania mieszanek betonowych w zakresie zgodnym z § 13.1-4 tego rozporządzenia.
Tabela 1. – standardy emisyjne
Instalacja do termicznego przekształcania odpadów biodegradowalnych w kogeneracji spełnia standardy zawarte w rozporządzeniu Ministra Środowiska z dnia 22 kwietnia 2011r. w sprawie standardów emisyjnych z instalacji (Dz. U. Nr 95, poz. 558), wg którego wielkości dopuszczalnych stężeń zanieczyszczeń w gazach odlotowych z nowych instalacji termicznego unieszkodliwiania odpadów przedstawia tabela 1 (zgodnie z załącznikiem nr 5 rozporządzenia). W/w standardy odnoszą się do warunków umownych (temperatura 273 K, ciśnienie 101,3 kPa i gazu suchego, tj. o zawartości pary wodnej nie większej niż 5g/kg gazów odlotowych, przeliczonych na 11% tlenu w spalinach). Wytwarzany popiół, jako odpad wtórny zgodnie z & 5 pkt 1 Rozporządzenia Ministra Gospodarki z dnia 21.03.2002 r., (Dz.U. nr 37 poz. 339 z późniejszymi zmianami) w sprawie wymagań dotyczących prowadzenia procesu termicznego przekształcania odpadów będzie zawierać poniżej 3% węgla organicznego i może być wykorzystany do wytwarzania mieszanek betonowych w zakresie zgodnym z § 13.1-4 tego rozporządzenia.
Lp. | Substancje | Standard emisyjny przy 11% tlenu w spalinach (mg/mgu3) |
1 | Pył | 10 |
2 | Węgiel organiczny (3) | 10 |
3 | Chlorowodór (HCL) | 10 |
4 | Fluorowodór (HF) | 1 |
5 | Dwutlenek siarki (SO2) | 50 |
6 | No, wyrażone jako (NO2) | 200 |
7 | Kadm (Cd) | 0,05 |
8 | Tal (Tl) | 0,05 |
9 | Rtęć (Hg) | 0,5 |
10 | Antymon | 0,5 |
11 | Arsen (As) | 0,5 |
12 | Ołów (Pb) | 0,5 |
13 | Chrom (Cr) | 0,5 |
14 | Kobalt (Co) | 0,5 |
15 | Miedź (Cu) | 0,5 |
16 | Mangan (Mn) | 0,5 |
17 | Nikiel (Ni) | 0,5 |
18 | Wanad (V) | 0,5 |
19 | Dioksyny i furany | 0,11) |
1) dla dioksyn i furanów standard emisyjny wyrażony w ng/mu3.
Zgodności z zaleceniami BAT oraz przepisami krajowymi
Instalacja termicznego przekształcenia odpadów jest instalacją spełniającą wymagania wynikające z ustaw, które stanowią podstawy prawne dla wdrożenia dyrektywy IPPC (Integrated Pollution Prevention and Control) nr 96/61/WE z 24 września 1996r., w tym najlepsze dostępne techniki (BAT – Best Available Technique) zawarte w dokumencie referencyjnym (BREF) dla spalarni odpadów (WI – Waste Incineration).
W technologii termicznego przekształcenia odpadów uwzględnione zostały następujące „Priorytety”:
- w procesie termicznej utylizacji odpadów, zapewniony jest dwustopniowy system spalania odpadów – pierwszym etapem jest proces pirolizy (odgazowania), gdzie rozkład termiczny zachodzi bez dostarczania tlenu, drugim etapem jest dopalanie gazów pirolitycznych w komorze dopalania z nadmiarem tlenu,
- w procesie termicznej utylizacji odpadów spełniony jest warunek utrzymania spalin powstających we właściwym procesie spalania w temperaturze powyżej 850°C przez ponad 2 sekundy, nawet w najbardziej niekorzystnych warunkach,
- proces termicznego przekształcenia odpadów przebiega przy termodynamicznych i chemicznych parametrach środowiska reagującego, eliminujących warunki niepożądanych oddziaływań na proces spalania, w wyniku których mogą powstawać substancje szkodliwe dla otoczenia,
- w procesie termicznego przekształcenia odpadów zminimalizowany został wpływ zawartej w odpadach siarki, azotu, chloru, sodu, fosforu, potasu, rtęci, ołowiu, cynku, cyny, miedzi i innych metali ciężkich metodami „pierwotnymi” na zawartość powstałych w trakcie spalania tlenków siarki, azotu oraz par metali ciężkich i niektórych związków metali alkalicznych,
- w procesie termicznej utylizacji, ograniczone zostało niekorzystne dla żywotności powierzchni ogrzewalnych kotła, oddziaływania związków chloru i siarki oraz osadzanie się na nich kondensujących się par metali ciężkich i metali alkalicznych oraz ich związków z siarką i chlorem, co doprowadziło do zmniejszenia zabrudzenia powierzchni ogrzewalnych i utrzymania współczynników przejmowania ciepła przez wodę lub parę wodną na początkowym poziomie,
- w procesie termicznej utylizacji, metodami „pierwotnymi” ograniczona została ilość wynoszonego z komory spalania lotnego koksiku, który stanowił stratę niecałkowitego spalania, obniżającą sprawność termodynamiczną instalacji o kilka procent, poprzez katalityczne dopalanie go w strefie przypłomiennej płomienia olejowego,
- proces termicznej utylizacji odpadów przy pomocy zastosowanej technologii, zminimalizował oddziaływanie procesu utylizacji na środowisko poprzez ograniczenie emisji substancji gazowych (S02, NOx, CO, HCl, HF, Corg) do atmosfery, zawartość metali ciężkich i karbonizatu w popiele do gleby, oraz fenoli i innych ciekłych substancji szkodliwych, zawartych w ściekach do gleby.
W odróżnieniu od powszechnie stosowanych technik termicznej utylizacji odpadów, zastosowana technologia metodami „pierwotnymi”, w bardzo szerokim zakresie substancji szkodliwych dla otoczenia zmniejsza intensywność ich powstawania.
Instalacja do termicznej utylizacji odpadów oparta o zastosowaną technologię jest najbardziej efektywną, pod względem termicznej przemiany energii chemicznej odpadów w użytkową energię cieplną, oraz pod względem ilości powstających w trakcie spalania substancji szkodliwych dla otoczenia.
Zastosowana technologia termicznej przemiany substancji odpadów, oraz metoda i droga przejścia substancji wyjściowej w gazowe produkty spalinowe i stałe produkty popiołu jest ciągłym procesem rozpoczynającym się od suszenia poprzez szybką pirolizę, spalanie gazów pirolitycznych, spalanie karbonizatu, a skończywszy na dopalaniu lotnego koksiku i resztkowych gazów palnych takich jak np. CO, przebiegającym w procesie termicznej przemiany bez straty energii cieplnej, przy istnieniu węzłów schładzających. Przemiana przebiega przy maksymalnej sprawności termicznej. Proces termicznej przemiany przebiega przy parametrach termo dynamicznych ( ciśnienie, temperatura ośrodka reakcyjnego) i chemicznych (skład chemiczny i koncentracji reakcyjnych substancji takich, jak: CO, H2, CH4, C2H2 itd. oraz koncentracja tlenu i azotu) gwarantujących całkowite i zupełne spalanie gazów pirolitycznych przy ograniczonej emisji NOx, Corg i WWA. Ograniczenie mechanizmu powstawania NOx podyktowane jest doborem liczby nadmiaru powietrza oraz temperatury tej strefy komory, w której przebiega proces spalania na poziomie ( <1350°C) gwarantującym niską szybkość powstawania NOx, Corg i WWA.
Zastosowana technologia poprzez wprowadzanie węglanu wapnia do początkowej strefy termicznej przemiany odpadów umożliwia obniżenie zawartości SO2 już w gazach pirolitycznych w fazie termicznego rozkładu zarówno substancji odpadów jak i węglanu wapniowego, które generują lotne produkty siarki i wapnia tworzące w oknie temperaturowym 850-950°C neutralny produkt, jakim jest gips. Pozostała w karbonizacie siarka podawana jest do złoża fluidalnego, gdzie w obecności stałej fazy węglanu wapnia w procesie spalania karbonizatu tworzy również gips. Regulowany w złożu fluidalnym czas przebywania ziaren karbonizatu oraz jego koncentracja, jak również kontrolowana temperatura złoża i koncentracja tlenu w gazie fluidyzacyjnym, umożliwia całkowitą kontrolę nad stopniem wypalania karbonizatu w złożu. Dzięki realizacji powyższego zakresu kontroli nad procesem wypalania karbonizatu ze złoża fluidalnego uzyskujemy popiół całkowicie pozbawiony części palnych. Uzyskany popiół jest surowcem do produkcji materiałów budowlanych, zawierającym poniżej 3% części palnych w postaci Corg. Przy realizacji termicznej utylizacji odpadów zastosowanej technologii znacznej redukcji podlega ilość par metali alkalicznych i metali ciężkich. Redukcja par metali odbywa się przy pomocy wychłodzonych powierzchni kształtowych, na których przebiega proces kondensacji.Termiczna utylizacja odpadów przy pomocy instalacji, w której realizowana jest technologia termicznej przemiany jest technologią, w której w najbardziej efektowny sposób, z najwyższą sprawnością termiczną przebiega proces przemiany substancji organicznej przy minimalnych wielkościach emisji substancji szkodliwych do otoczenia.
Proces obniżania emisji substancji szkodliwych do otoczenia przy pomocy metod „pierwotnych” realizowanych przy pomocy zastosowanej technologii jest najtańszą z możliwych do realizacji znanych metod energetycznego recyklingu odpadów.Poniesione koszty na realizację działań, w trakcie procesu termicznego przekształcania (pirolizy i spalania), które doprowadzają do znacznego obniżenia emisji do otoczenia są zdecydowanie tańsze od sposobów realizujących oczyszczanie spalin z substancji szkodliwych na wylocie z kotła tzw. metodami wtórnymi. Realizowane w technologii obniżenie ilości powstających substancji szkodliwych przebiega samoistnie według ściśle zaplanowanej technologii suszenia, pirolizy i spalania bez żadnych dodatkowych nakładów finansowych.
Z powyższych przesłanek można w sposób zdecydowany wykazać, że termiczna utylizacja odpadów biodegradowalnych przy pomocy posiadanej technologii zapewnia całkowite bezpieczeństwo ekologiczne środowiska położonego w bezpośredniej i dalszej odległości od instalacji. Środowisko powietrza jest wolne od wszelkich zanieczyszczeń szkodliwych dla organizmów żywych, wszelkiej uciążliwości zapachowej i słuchowej. Są zabezpieczone wszelkie warunki i priorytety środowiskowe i techniczne.